Carbon Fiber. The unique woven material has become synonymous with high-performance in the last few decades. Initially developed for military and aerospace applications, the material can be solid while maintaining light weight. Carbon fibre, as we currently know, it is composed of two parts: a matrix and a reinforcement. This is commonly referred to as carbon-fibre reinforced plastic or polymer. In CFRP, the reinforcement is carbon fibre, which provides its strength. The matrix is usually a polymer resin, such as epoxy, to bind the reinforcements together. The woven material exists from experimental work in the 1960s to find alternative raw materials, ultimately leading to the introduction of carbon fibres made from a petroleum pitch derived from oil processing. These fibres may also be derived from Rayon or Polyacrylonitrile (PAN for short.)
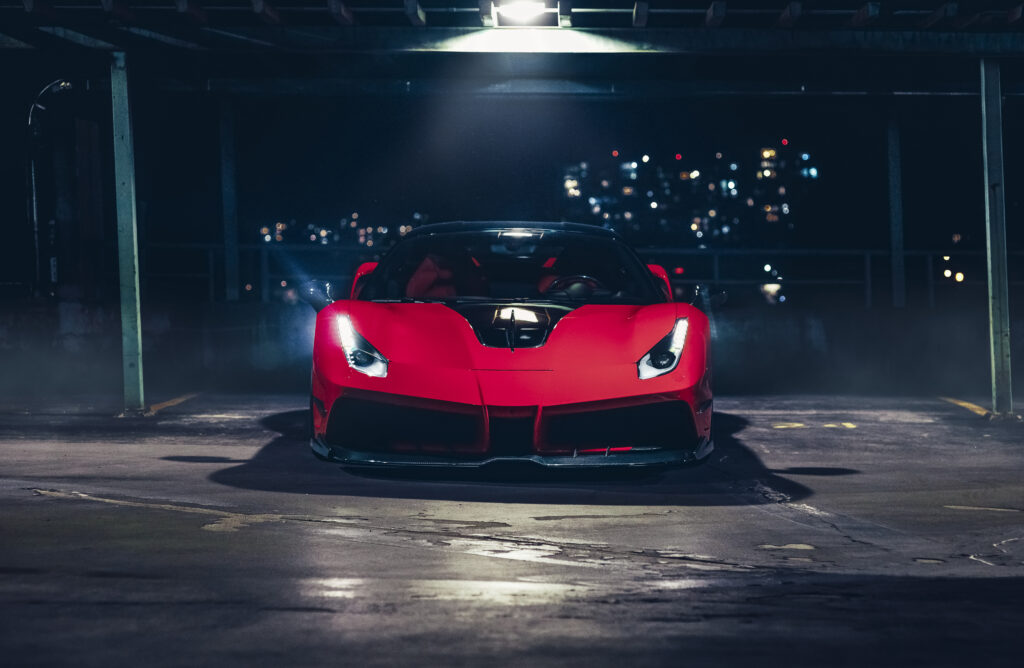
After much success in the aerospace industry, it was used as a structural material for blades, props and bulkheads. Rolls-Royce began using the textile for fan assemblies that control airflow on their jet turbine engines powering many commercial and cargo airplanes over the decades. In 1981 after seeing one such fan during a factory tour, John Barnard as chief engineer, helped Mclaren debut its MP4/1 open-wheel car built for Formula 1 competition (a technicality as the Lotus 88 that initially theorized the idea was disqualified at the season opener due to a rule breach), becoming the first car ever to be produced with a carbon fibre monocoque. The unique material wound its way further into the automotive industry through supercars that turned wild powerplants into insane speed. Ferrari’s F40 would be the first to wear body panels produced from carbon. As far back as 1971, Citroen’s collaboration with rubber manufacturer Michelin would yield carbon fibre wheels for the SM, helping it win the Rallye Du Maroc (Moroccan Rally.) Jaguar’s XJR-15 would be the first production car with a carbon monocoque chassis (the entire vehicle is produced from the composite.)
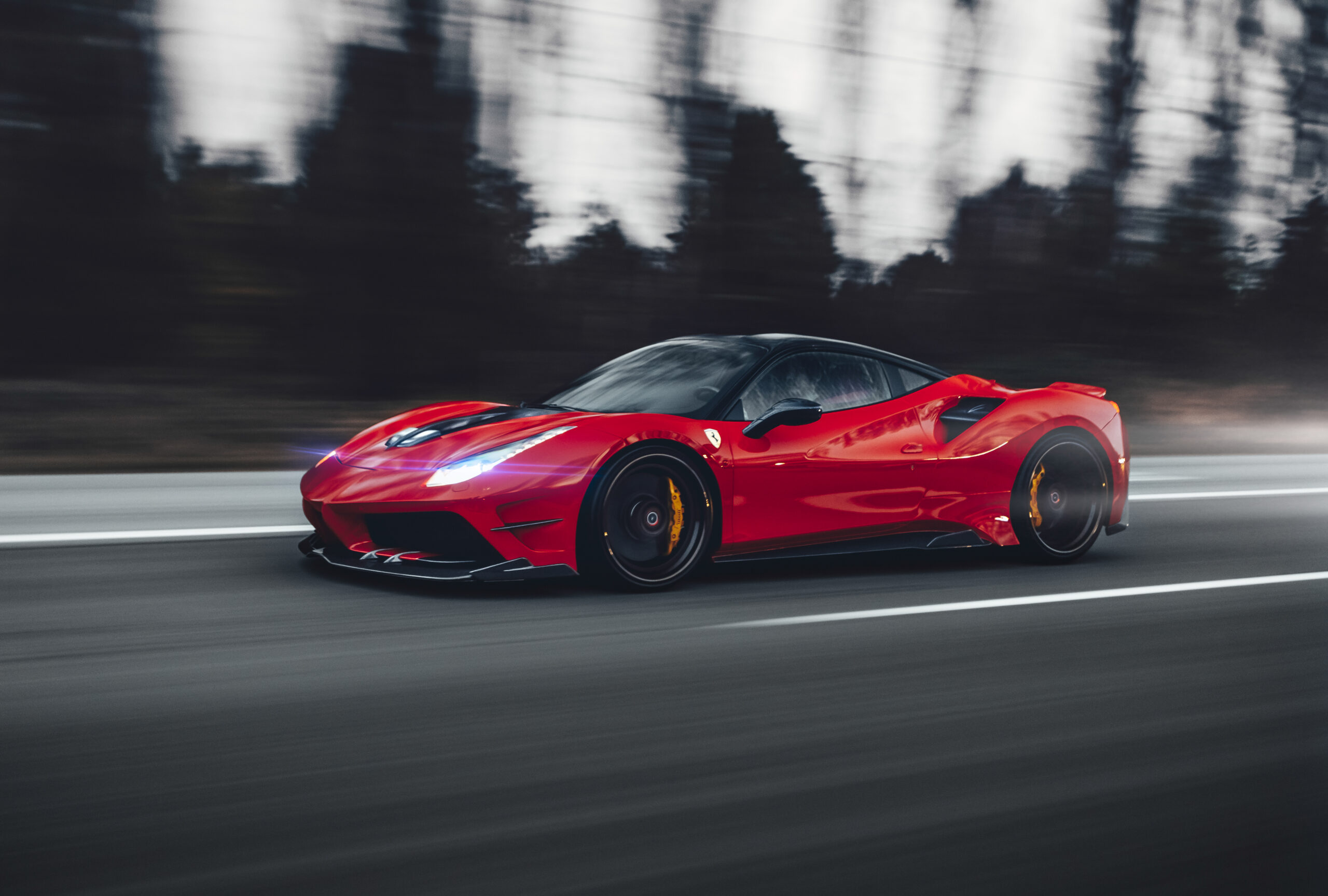
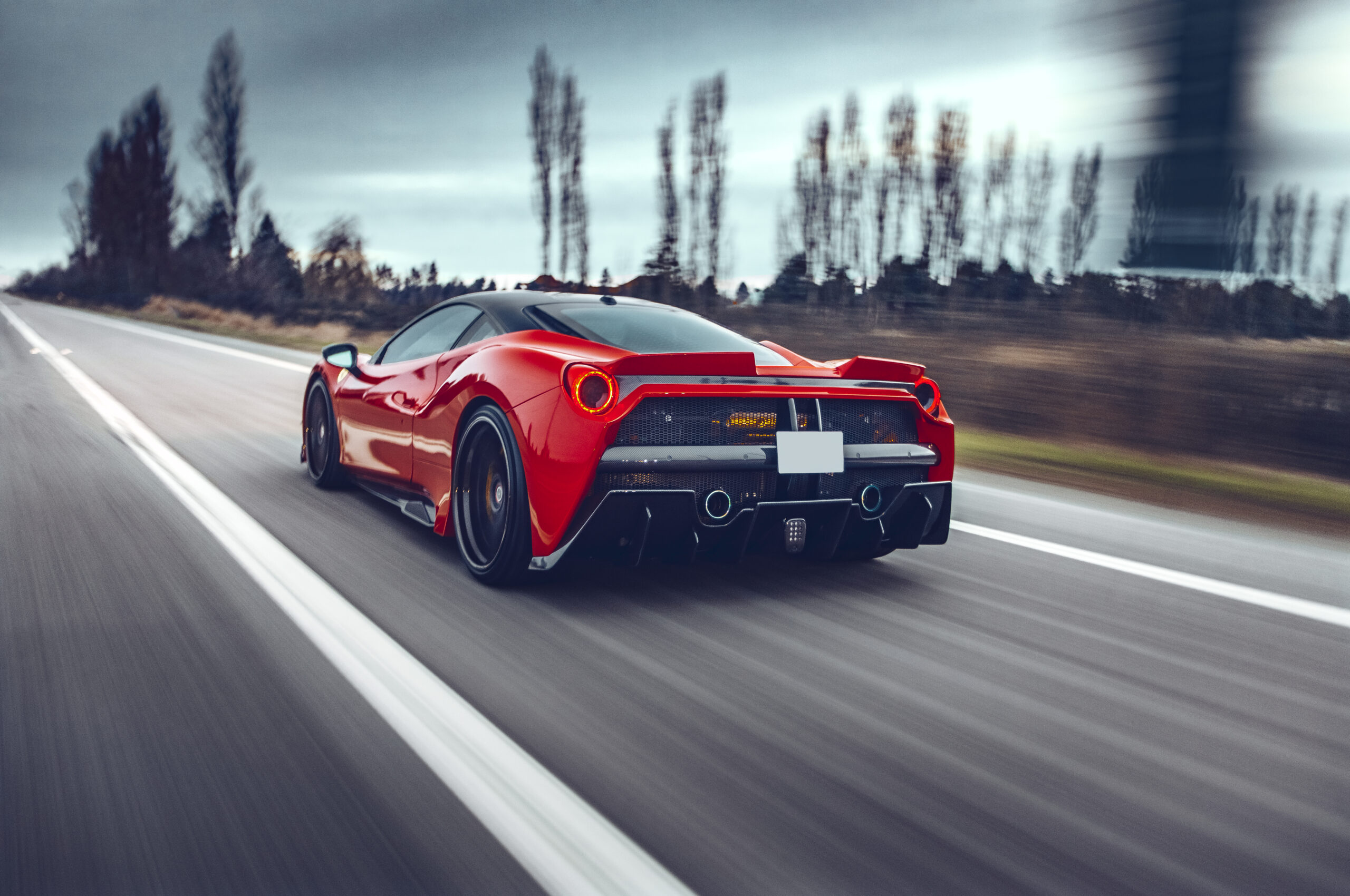
More recently, Lamborghini has developed a new way to use the material in manufacturing instead of as a weaved fabric. The new process known as Forged Carbon takes small pieces of the material that is instead pressed into a resin. This helps to keep a higher fibre volume, which also means more strength. The forged parts certainly look more unique in comparison to the traditional weave.
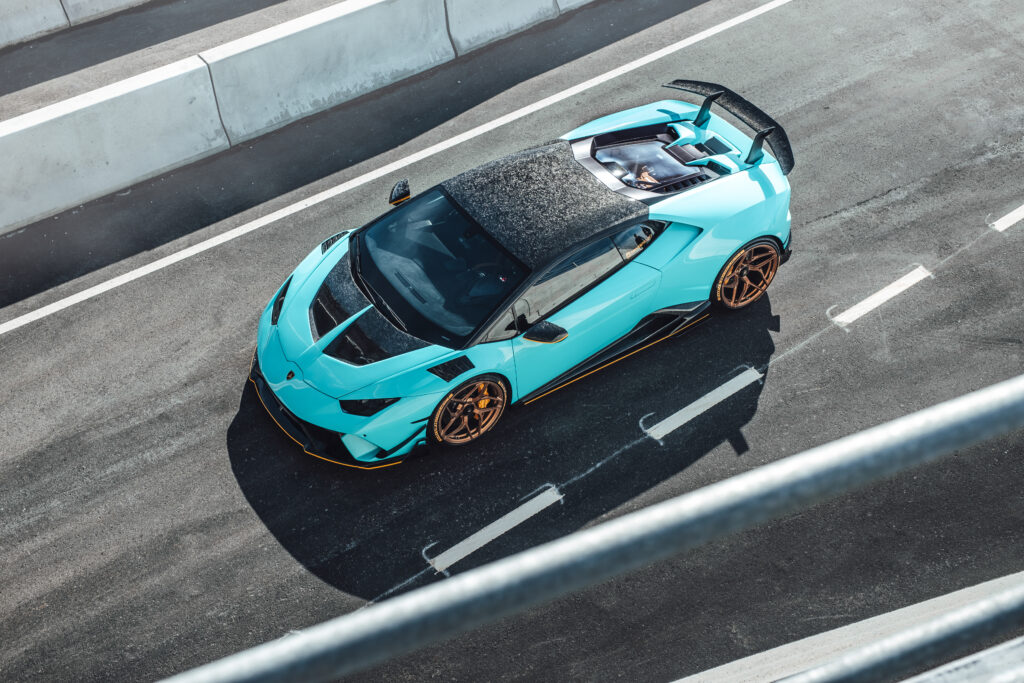
Some of us may not have the luxury or option to have the lightweight material grace our street machine, and in some cases, there aren’t any mainstream options for such a thing. Carbon can be surprisingly costly simply because of the labour involved in producing components. When that’s the case, there’s a little shop known as FinalRare. Founded by Michael Wong of MasterWerke Design Technik and Ken Pham, they share over 30 years of combined automotive custom and design experience. There are no signs present or advertisements found anywhere. Their work speaks for itself with every unique ride they’ve laid their hands on; they are capable of one-off projects and proficient in repairing composites. Clients with many of Ferrari’s modern stallions such as the SF90 and 488 Pista have graced the shop for much needed repairs on parts that met an untimely demise on Vancouver streets.

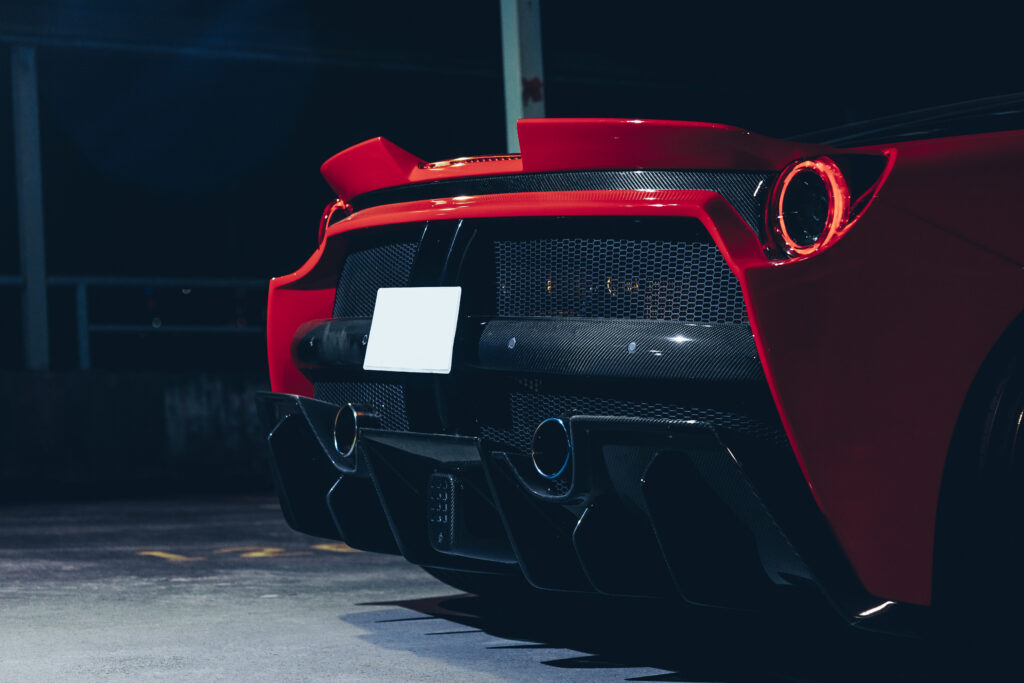
The shop has taken on a variety of clients’ visions to perfect their labour of love. Various Lamborghini’s draped in the chunks as mentioned above of carbon have had the pleasure of going on a diet courtesy of FinalRare. If all the carbon wasn’t enough, Kevin Gordon of Driven Project’s Huracan Performante received one-off canards, a front splitter with additional winglets and a unique front bumper with plenty of exposed forged carbon. The entire roof was covered with the extraordinary textile to match the rear diffuser and spoiler section. New mirrors that adorn the Huracan’s doors are also not something seen on the shelf, matching the sideskirt splitters perfectly. Even the front fenders have been fitted with a set of vents akin to a GT3 racer.
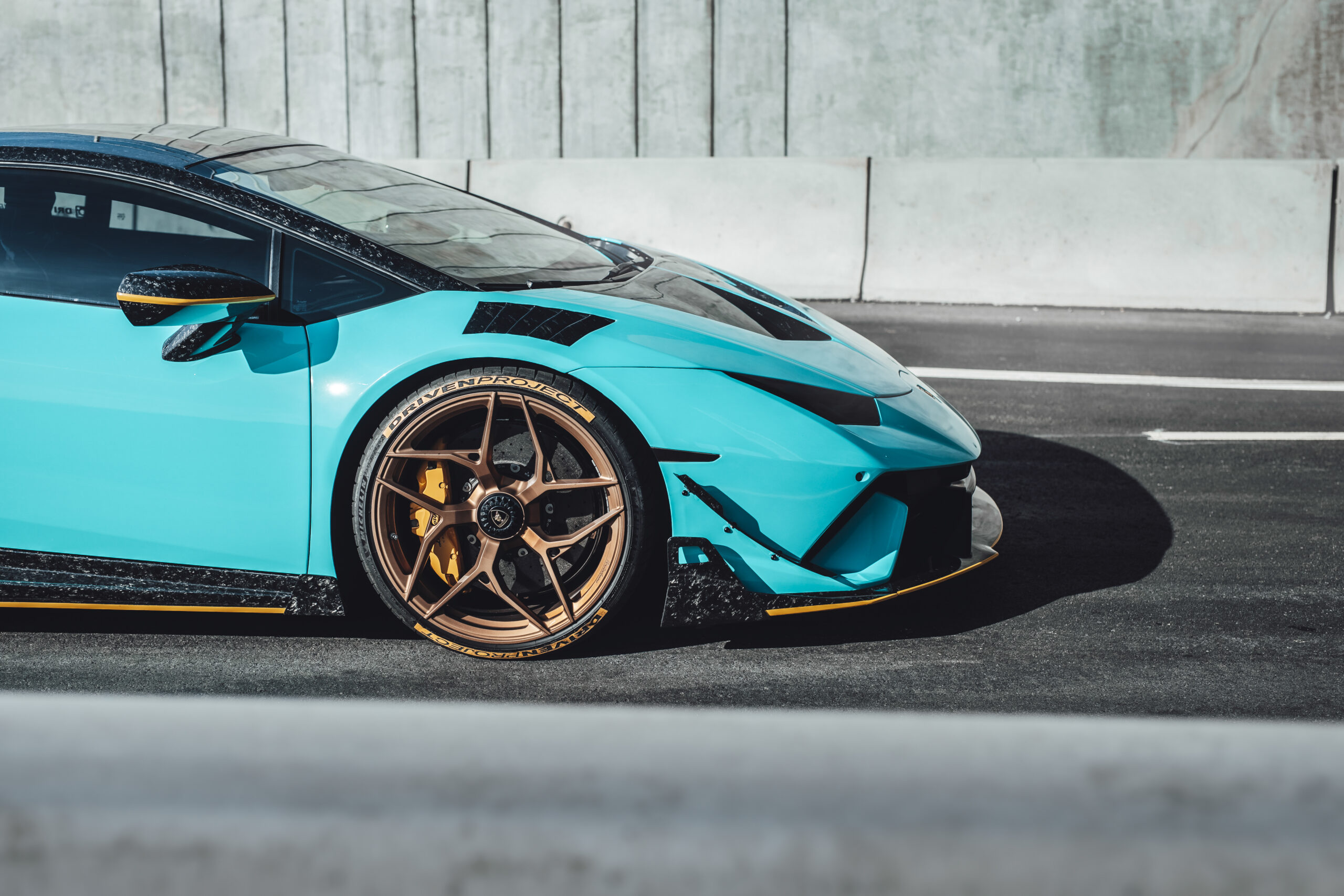
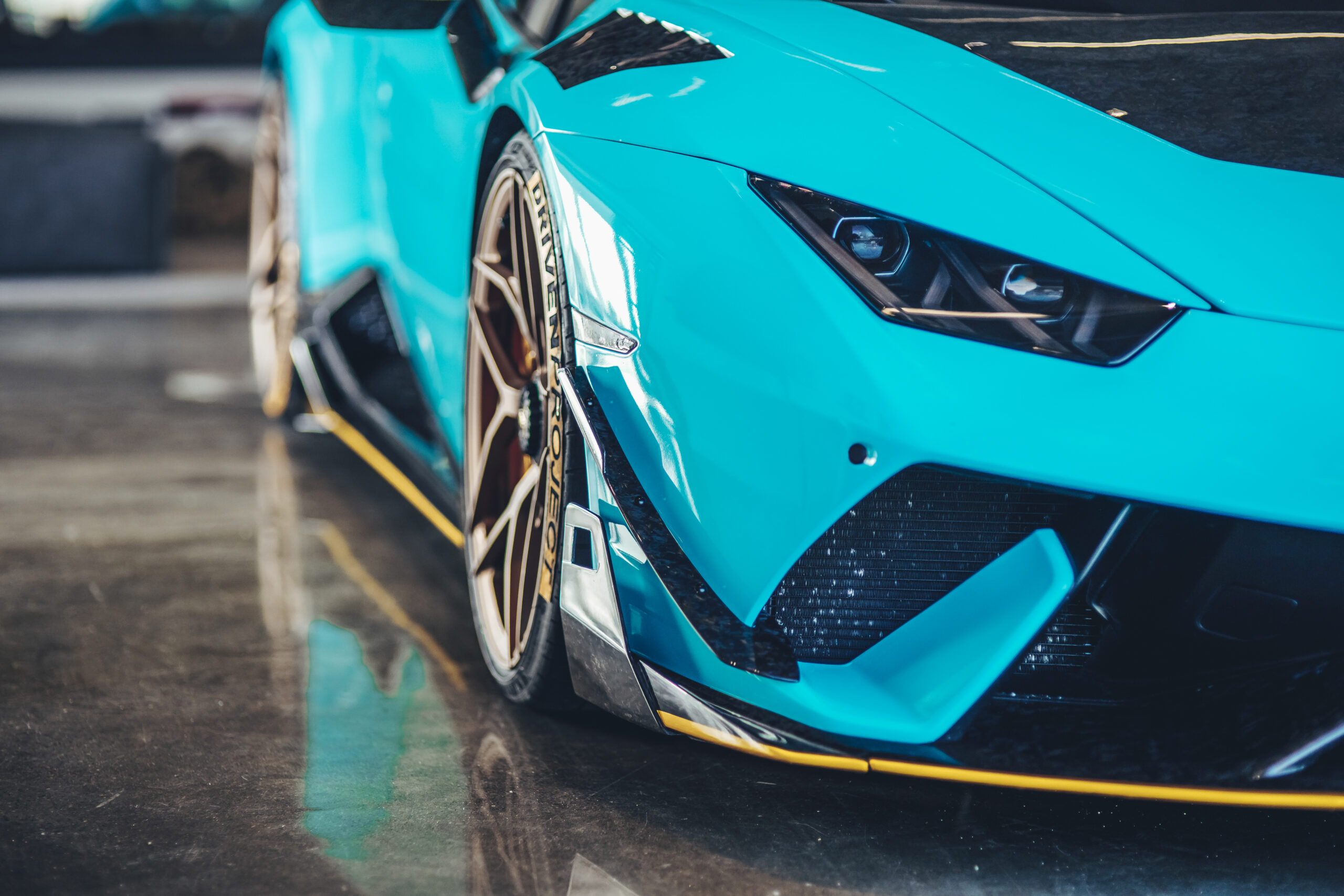
As mentioned previously, FinalRare is no stranger to working their magic on Ferrari’s’. Maranello’s controversial 488 may already be extraordinary to plenty of delighted of fans, however, some may feel like they need just that little more “oomph” like one of their recent clients. Featuring the Misha Designs aero kit that adds aggressive front and side splitters with special fins drawing inspiration from Ferrari’s famed FXX line of track-only beasts. The front bumper features additional venting for heat extraction while the rear cuts away majority of the center section for the same purpose. Skid plates and additional reinforcement were added to high stress and heavy contact areas of the front bumper and side skirts to ensure they stay together. The swan neck-like door mirrors were reskinned in matching carbon weave to accentuate the aero kit further.
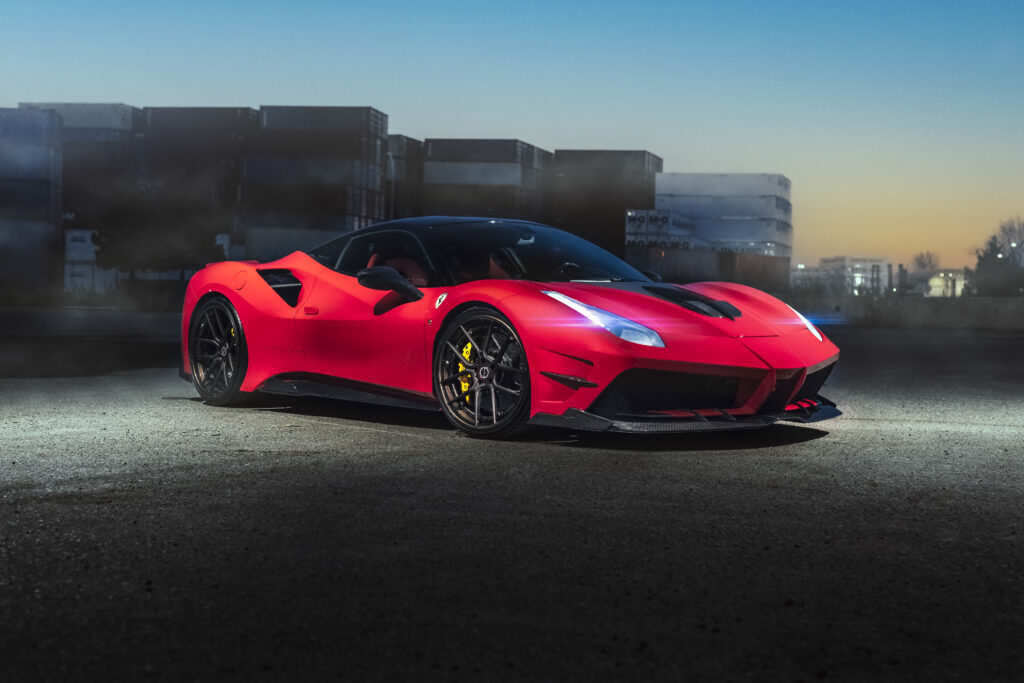
The most exquisite piece still in the works is a fascinating project. A Ferrari 458 Italia adorned with Liberty Walk’s Silhouette Works GT kit. The client initially chose the aero in fibreglass; however, the client felt the need for something more unique. As a result, every panel of the 458 has now been recreated in carbon, integrating the widebody kit within. Not only has the Ferrari been resculpted, but each panel was also meticulously set to Ferrari’s standards and ensured the weave of the carbon spread throughout uninterrupted unless on purpose. FinalRare has shown the quality of their artistry on every panel, speaking volumes about their passion for the craft.
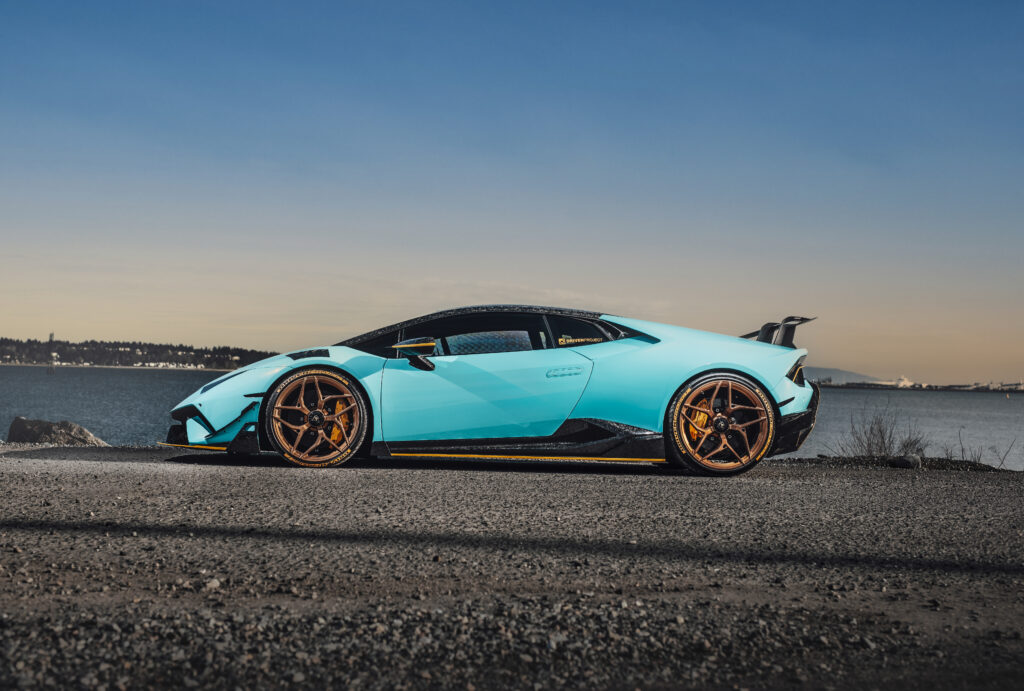
If you’re considering a novel addition of carbon to your machine, FinalRare can certainly accommodate your needs.